
Vegetable oil lubricants will always have to include an antioxidant such as TBHQ at levels of 0.1 percent (10x higher than in foods) to help the oil resist oxidation. The OSI measurement refers to the onset time of oxidation while bubbling air through the oil at 110 oC. A typical high oleic canola oil will have an oxidative stability index (OSI) of 24 hours, while its regular counterpart has an OSI of approximately seven hours. However, high-oleic acid oils (greater than 75 percent oleic acid), including canola, sunflower and soybean, have an increased oxidative stability. Most vegetable oils such as canola or soybean oils have cloud points between -10 oC and -20 oC, which is not considered truly low-temperature performanceĮven though vegetable oils have higher Vis and viscosity than mineral oils, all vegetable oils suffer from lower chemical stability. It is possible to create vegetable oils with very low pour points by randomising the oil using short chain or hydroxylated fatty acids, which interfere with crystal formation (nucleation inhibitor). Most vegetable oils such as canola or soybean oils have cloud points between -10 oC and -20 oC, which is not considered truly low-temperature performance. Low temperature stability is measured by the cloud point of the oil, which is less than -40 oC for cold-weather oils. However, increases in viscosity at lower temperatures are somewhat problematic, with the added issue of possible crystallisation. Vegetable oils, being an ester, have higher Vis than either mineral oil or synthetic oils.
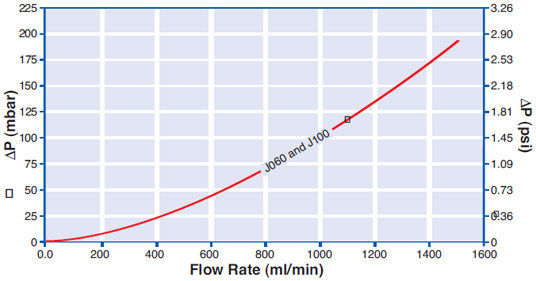
The more constant viscosity-temperature profile of the synthetic oil is more desirable. These are two characteristics best avoided in a lubricating oil. Notice, though the massive increase in viscosity for the mineral oil at -20 oC, and the larger decrease in viscosity at 100 oC. Notice that Oil A, a mineral oil, and oil B, a synthetic PAO oil, have the same viscosity at 40 oC, and would therefore be sold as the same oil. See the example in the table below.Ĭomparison of viscosity characteristics as a function of temperature between a mineral oil (A) and a PAO based synthetic oil (B).
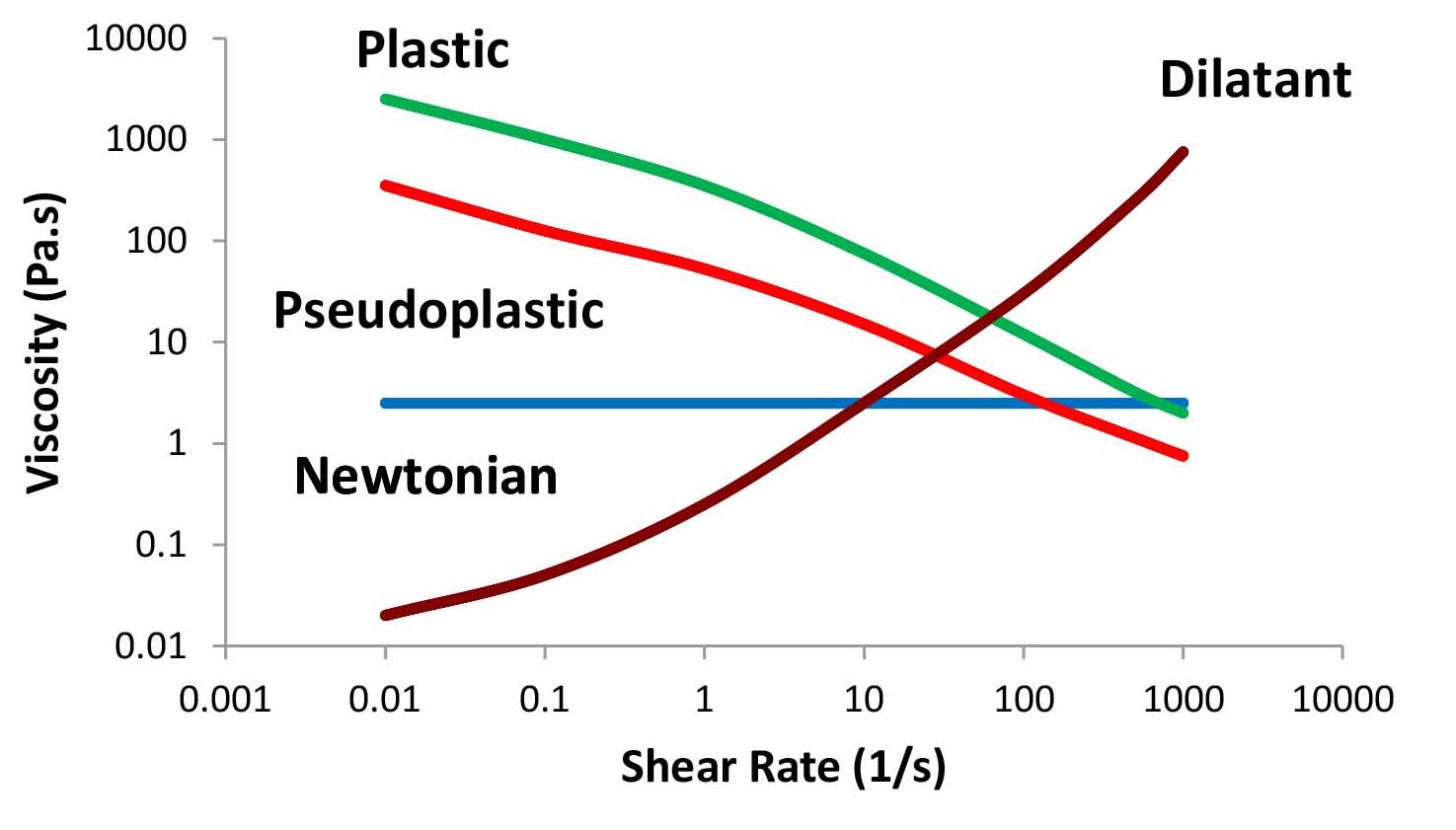
The unit cSt refers to the kinematic viscosity (dynamic viscosity/density in units of cm 2/s). For example, in the trade, a 10wt oil can have viscosities between 25cSt and 45cSt at 40 oC (standard temperature), but obviously, a 25cSt vs a 45cSt oil will have very different base properties and performance.

In my view, this is a very poor classification scheme. Most of the time, this viscosity is reported as the oils’ “weight”. Oils are classified in families of viscosity. This consideration for VI is important and can be confusing when, for example, buying two oils of the same viscosity classification. Mineral oils have VIs below 100, PAO synthetic oils around 150, while high-oleic canola oil has a VI of 220. High performing suspension oils sometimes have Vis in the range 300-400. Most lubricants, food grade or not, are based on mineral or synthetic oils of specific viscositiesĪ viscosity index below 100 is considered low, while a VI higher than 200 is considered very high. You do not want your oil to seize at low temperatures but also not to lose all viscosity at higher temperatures. The key characteristic of a high VI oil is its ability to withstand decreases in viscosity as a function of increasing temperature.

The viscosity index of an oil refers to the difference in viscosity between 40 oC and 100 oC. Polymerisation of this alpha-olefin results in the formation of synthetic oils of different viscosities and with added benefit of higher viscosity index than mineral oils. The most common monomer used in synthetic oil manufacture is alpha-olefin, a six-carbon primary alkene. Synthetic oils are usually of higher purity and offer thus a higher performance. Most lubricants, food grade or not, are based on mineral or synthetic oils of specific viscosities. This would lead to a catastrophic failure of the machine’s moving parts. If the moving metal surfaces come too close, metal-to-metal contact will lead to surface damage (scarring), and if the heat becomes high enough, surfaces can melt and fuse. The main functions of a lubricant are to decrease the friction coefficient between moving surfaces, thus improving on machine performance with smaller energy inputs, as well as to help dissipate frictional heat.
